Environmental Policy
Introduction
Stoane Lighting is an employee-owned specialist manufacturer of architectural lighting equipment based in Edinburgh. We recognise the importance of a sustainable approach to manufacturing and of quantifying environmental impacts. This allows us to keep track of our impacts and to guide decision making aimed at reducing them.
Purpose
The scope of this policy is to set our current efforts and objectives
regarding the sustainability of products and operations within our company,
with the aim of continually improving them, so that we can ensure that our actions
and the decisions we make are always driven by sustainability. Specifically, we commit to:
Comply with applicable laws regulating sustainability in lighting
Minimise our impact on the environment
Maximise the effective use of
resources
Promote responsible environmental behaviour among our staff and for
company-level decisions
Offer circular solutions and support projects throughout their lifetime
Collaborate and participate in activism and knowledge-sharing
initiatives
Company Sustainability
All manufacturing ultimately harms.
Stoane Lighting examines all its processes to minimise this harm. Our equipment is manufactured to order only: the resources and energy required to manufacture products are only invested when there is a specific demand. This reduces the waste from typical manufacturing business models and our impact. Waste generated is minimised and dealt with responsibly through use of third-party approved recycling companies. The company electricity supply comes from 100% renewable sources, and we make sure that we make an efficient use of that electricity for all our in-house processes.
We have invested in the use of electric vehicles for local supply chain deliveries and we are committed to implement ways to facilitate the use of electric vehicles by our employees, such as installing charging points on site. Employees are aware of our obligations and responsibilities and they play a fundamental part in fulfilling them.
We are an annually audited member of the Lighting Industry Association in the UK who make sure that our systems, practices and equipment comply with all necessary standards.
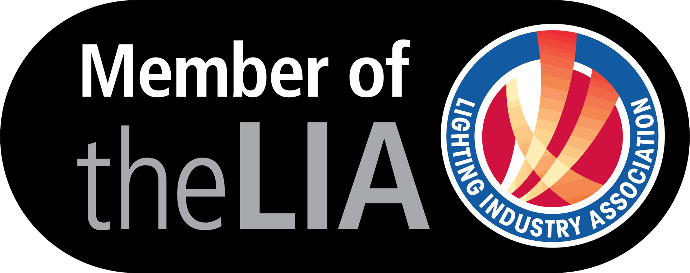
We are also a member of a WEEE recycling scheme. All products sold in the UK market can be picked up and recycled responsibly by our recycling partners. Their practices can potentially recover up to 98% of the materials used in the manufacturing of lighting equipment.
We will always give full cooperation to bodies administering environmental legislation.
We recognise however the importance of certifying a company’s environmental performance by accredited bodies. Stoane Lighting have been a proud certified B Corp since 2020 and in 2024 we obtained our re-certification and increased our score.
We are also building a company-centred system to quantify our own Scope 1, 2 and 3 Greenhouse Gas emissions. Our aim is to find hotspots in our organisational emissions and reduce them.
We believe in the
importance of keeping track of Scope 1, 2 and 3 emissions not only to set
targets to get closer to Net Zero, but also to understand more about our
own activities and where we can apply changes to achieve more sustainable
practices.
Product Sustainability
Our products are manufactured to last; robust mechanical design of components ensures that equipment produced lasts and does not need to be prematurely replaced. They are designed to allow repair and upgrade of components so that they can be refurbished at the end of serviceable life rather than disposed of.
Our mission is to encourage repair of lighting equipment
rather than replacement and we actively seek to be challenged by our customers
to make this possible for them. That's why our luminaires are designed to be
disassembled easily. To encourage clients to consider the remanufacturing
option in projects, we also offer a remanufacturing service, where we can even
visit the client on site and carry out all necessary operations with minimal
disruption to the site’s activities.
We select components for our designs based on their efficiency, aiming for the most efficient light sources, power supplies and optical system. We also aim to provide the best technical data we can, to enable specifiers to be as accurate and concise with their schemes as possible. Building confidence in final results helps reduce over-lighting and all the short and long term environmental consequences of that.
Our aim is to reduce the use of plastic in packaging to zero and further, to use recycled cardboard packaging from goods inwards and neighbouring businesses to package our products. This is to minimise virgin materials consumed (even if recyclable) whilst avoiding damage to goods in transit.
We recognise the value of assessing environmental impacts of products and the importance of communicating this transparently to our clients. We comply with and improve upon the standards required under relevant legislation; right now, we employ the use of industry-led and lighting-specific assessment metrics, CIBSE TM65.2 and TM66, to quantify the embodied carbon and circular performance of our products. Every product in our catalogue is assessed against TM65.2 and TM66 and the reports are readily available to download on their product page.
Assessment and Reporting
We recognise the importance of rigorous environmental assessment. Just as crucial is being transparent and reporting our findings to our customers and to the wider lighting industry.
Discover
Life Cycle Assessment harmonisaton explained
In addition to embodied carbon and circularity assessments, we recognise the validity of environmental impact calculations through Life Cycle Assessment (LCA). We use this globally recognised method to calculate impacts and evaluate the choices we make for our products, considering a wide range of environmental areas and not just limiting our analysis to carbon emissions.
To carry out our LCA we follow standardised rules mandated by the relevant standards of the ISO 14040 series and luminaire-specific Product Category Rules (PCR). The most comprehensive PCR for luminaires, and also recommended by experts at LightingEurope, is PSR0014 ed.2 by the association PEP Ecopassport. We commit to follow these rules to promote and advance harmonisation of LCA in the lighting industry.
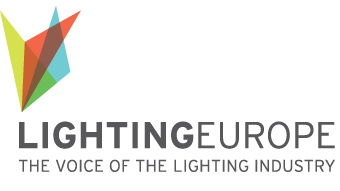
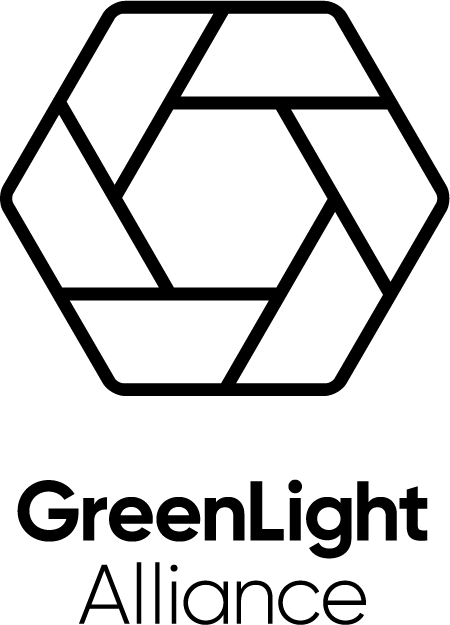
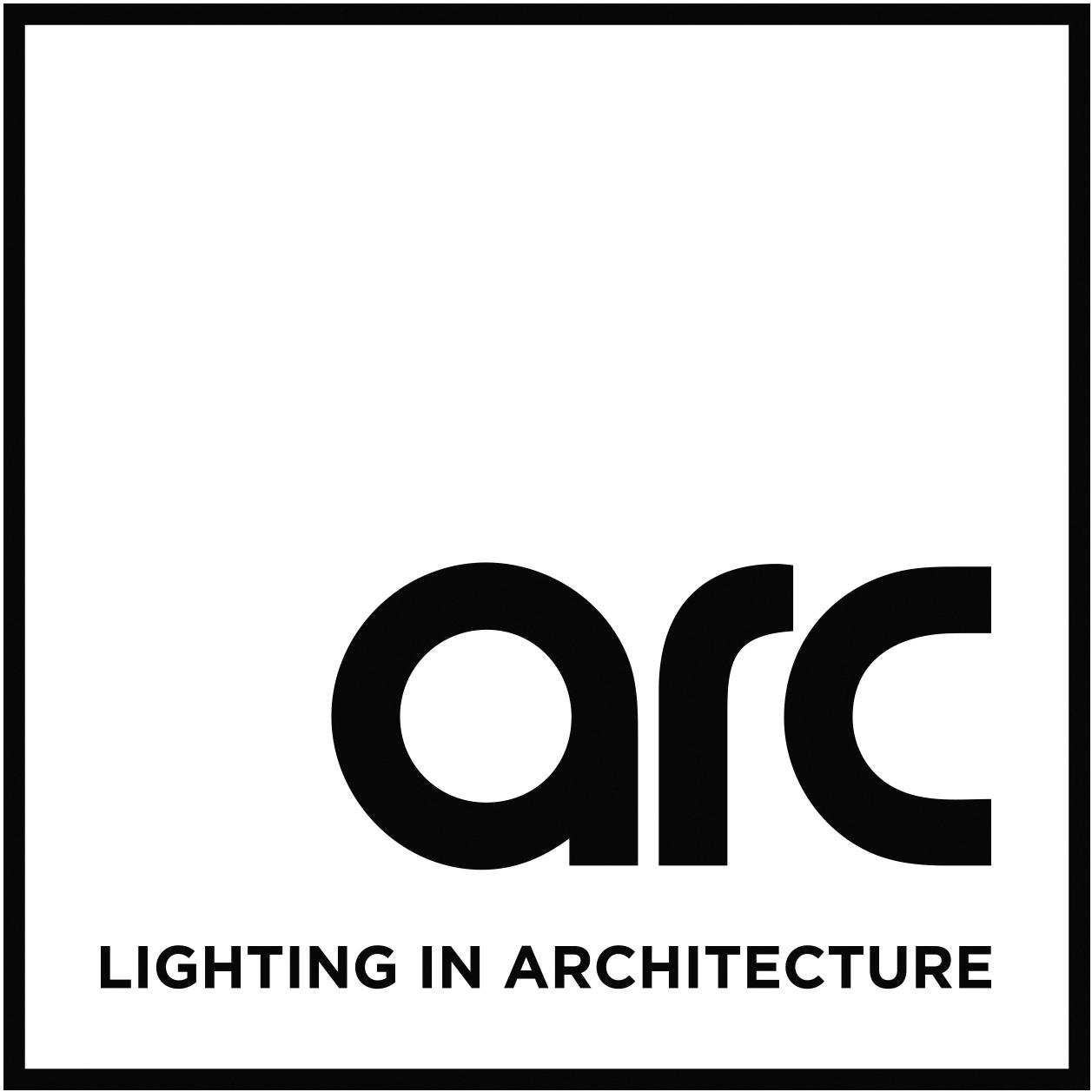
We commit to share LCA results transparently with our clients, as detailed in the dedicated section on LCA. The assessment results will be freely available as self-declared (or Type II, according to the ISO 14020 series definitions) environmental communications.
In addition to sharing the results of LCA carried out on our products following rules by PSR0014 ed.2, we also believe in the importance of having our assessments independently verified: this is why we also commit to produce Environmental Product Declarations (EPDs) for our product ranges.
Assessment as a Service
We recognise the challenges associated with environmental impact data collection, therefore we commit to supporting our clients by providing this information on our products.
We offer environmental assessment as a service, with a range of choices based on the type of methodology used and the focus of the assessment. This service can also be used to support client’s reporting requirements for project-level rating schemes (such as BREEAM).
Knowledge Sharing
We believe that in order to facilitate the adoption of more sustainable practices in the lighting industry, and ultimately make it possible to reach sustainability targets such as Net Zero, there is an urgent need for collaboration. This can effectively be achieved if members of the industry are aware and up-to-date on sustainability knowledge; if they know what to ask for and what information to provide.
This is why we are keen to share knowledge and awareness, by visiting design practices with our CPD offering, by participating in conferences and gatherings where we have a chance to talk about our experience in sustainable manufacturing and also by providing our contribution in industry press.
We wish to be challenged and educated on ways we can improve; tell us what we could do better.
Review
Our management strategy places importance in adhering to the processes outlined above, it includes rigorous review and corrective action procedures to foster a culture of continual improvement. Our approach is something we are proud of but wish to evolve and better.
All employees are encouraged to familiarise themselves with the company's environmental policy and are welcome to contribute on matters of continuous improvement.
Audit
We welcome external audit of our systems and procedures by any third party, be they customer or certification body. We can facilitate visits to our premises and will support information requests.