Technical: Finishing
We offer a huge flexibility in finishing options for our products
We can do this as all products are manufactured to order. With so much choice it’s important to understand the options and advantages/disadvantages of each approach.
Finishing luminaires is a critical step that not only enhances aesthetic qualities but also plays a vital role in ensuring product longevity and even performance. The choice of finish can dramatically impact the overall look and feel of a lighting fixture, as well as its ability to withstand various environmental factors.
There are several popular finishing techniques used for Stoane Lighting luminaires, each with their own unique characteristics:
Powder coating
Powder coating is available in a huge variety of colours (name your RAL code!) and textures, with matt white through to finishes that resemble an aged bronze and everything in between. It’s a robust finish that is often applied over anodised aluminium to provide protection to the aluminium from corrosion and scratching from handling. Powder is sprayed towards components where an electrostatic charge attracts and holds it until the component is baked in an oven and the powder melts to form the finished part.
Wet paint
In this case the paint is applied wet, it dries to a finish coat, sometimes in air with chemical curing or air drying and sometimes with heat. This option also offers a large flexibility in colour choice and options for metallic content and deep high gloss. We typically use this process for very matt black finishing on the insides of lamp tubes to reduce glare.
Plating
Plating involves applying a thin layer of metal, such as chrome, nickel, brass, or even gold to the luminaire surface. This can be an option where it is not economical to make the product completely out of that material. We have made gold plated Surf Type S before now.
Anodising
This process is used for aluminium components. It involves chemically treating the aluminium to create a protective oxide layer on its surface. Anodising can enhance the aluminium’s durability, corrosion resistance, and aesthetic appeal. Dyes can be added to the process to provide coloured finishes.
Nothing!
Sometimes not applying a finish can be the most appropriate. In these cases, the material might appear more ‘honest’, corrosion may even be desired. In these cases there are ‘finishing’ options which can include brushing and polishing. These approaches can have downsides, such as less favourable corrosion resistance or heatsinking performance.
Special
Specialist coatings can be deployed where our fittings are required to fit in with unusual environments, either because of artistic choices or because of harsher than usual environments such as marine, chlorine (pools), or high temperatures. These can include zinc passivating, specialist primers, textured finishes and specialist plating's such as precious metals.
Factors to consider when choosing a finish
When selecting a finish for a luminaire, speak to our Specifier Support team for guidance but several factors will be considered when assisting you:
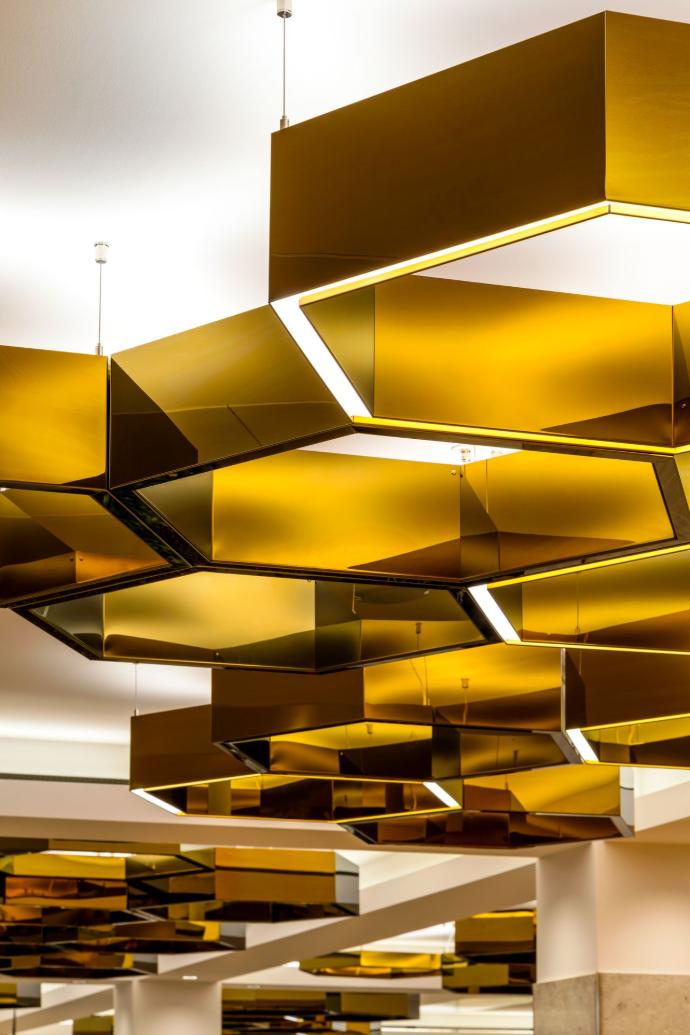
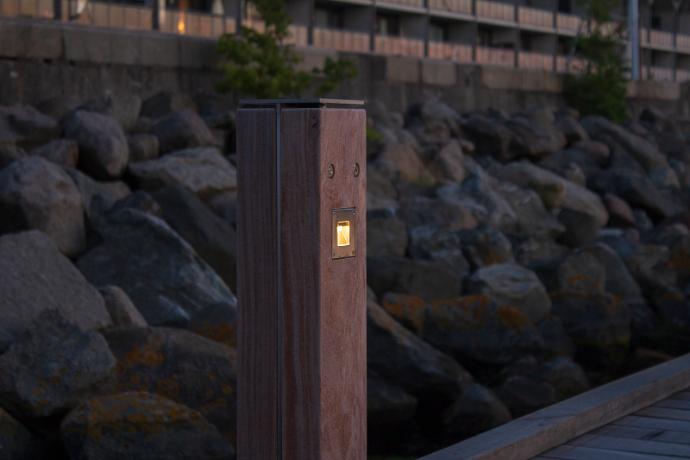
Aesthetic
How the product is to look, or what the product might need to be colour
matched to.
Durability
The finish should be able to withstand the expected environmental
conditions.
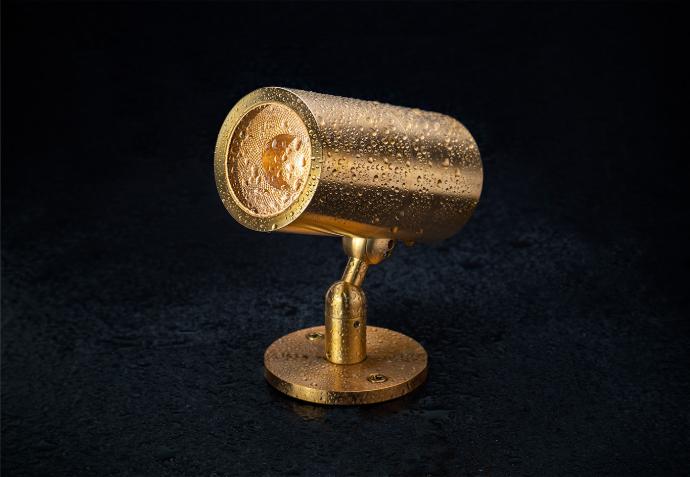
Impact on technical performance
Surface finish
(and sometimes colour too) can have a large impact on the heatsink performance
so technical characteristics such as heatsink size or lumen output may
need to be reassessed.
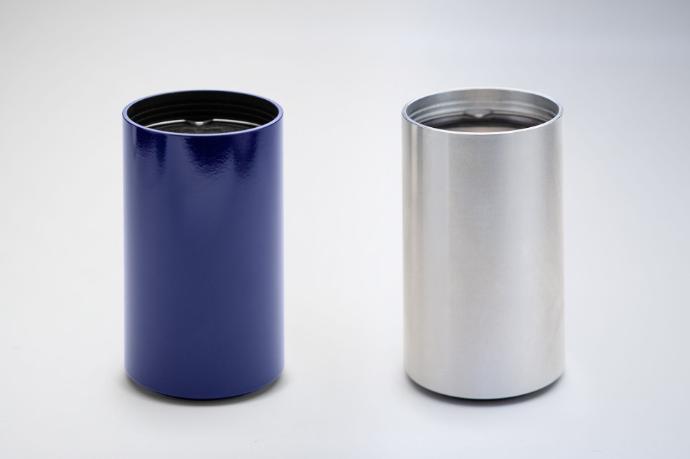
Cost
The cost of the finishing process can vary depending on the technique used
and the materials involved.
By carefully considering the factors above, we can help select the most appropriate finishing options to create high-quality, durable luminaires that meet the requirements and preferences of the project.
To help with the inevitable requests to assess options, we can prepare finishing swatches that can be sent out for assessment by client teams alongside other materials and textures.